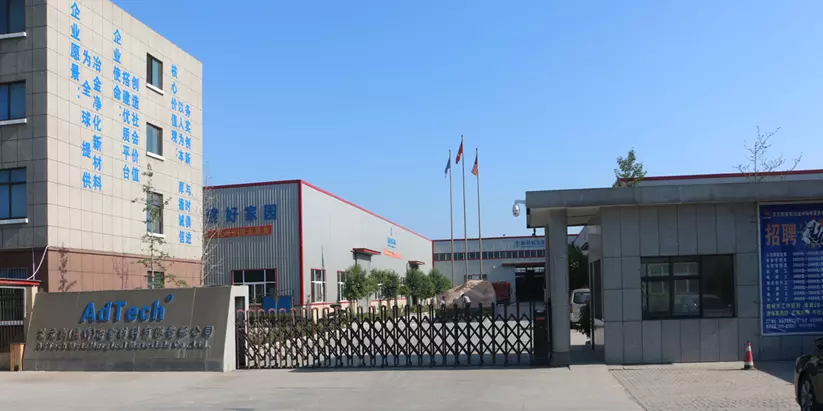
About Adtech
Adtech becomes the leader of Chinese aluminum liquid filtration equipment & CFF manufacturers in a short time. We focus on providing a one-stop solution of aluminum liquid purifying for global customers.
WELCOME TO JIANGJI DISTILLERY
We will present you a brand new world of Chinese Baijiu and its time-honored history
Are you old enough to enjoy?
This is part of our commitment to the responsible drinking of our consumers.
I have reached the legal drinking age.
REMEMBER ME
DO NOT CHECK THE ABOVE BOX WHEN YOU ARE USING A SHARED DEVICE.
BY ENTERING THIS WEBSITE YOU ACCEPT OUR
PRIVACY POLICY
JIANGJI encourages responsible drinking. Alcohol abuse is harmful for your health.
Adtech becomes the leader of Chinese aluminum liquid filtration equipment & CFF manufacturers in a short time. We focus on providing a one-stop solution of aluminum liquid purifying for global customers.